YUNNAN CNC Lathe – NINGJIANG High Performance Horizontal Machining Center TH(M)6350 TH(M)A6350 TH(M)6363 TH(M)A6363 THM6380 THM631000 – Maiouke
YUNNAN CNC Lathe – NINGJIANG High Performance Horizontal Machining Center TH(M)6350 TH(M)A6350 TH(M)6363 TH(M)A6363 THM6380 THM631000 – Maiouke Detail:
Item |
Unit |
TH(M)6350 |
TH(M)A6350 |
TH(M)6363 |
TH(M)A6363 |
THM6380 |
THM631000 |
|
Pallet worktable |
Worktable surface |
mm |
500×500 |
500×500 (Optional 500×630) |
630×630 |
800×800 |
1000×1000 |
|
B-axis index |
° |
0.0001°×3600000(Continuous) 1°×360(end tooth plate) |
0.0001°×3600000(Continuous) 1°×360(end tooth plate) |
0.0001°×3600000(Continuous) |
0.0001°×3600000(Continuous) 0.0001°×900000(Continuous) |
|||
Worktable rpm |
r/min |
15 |
12 |
10 |
5 |
|||
Pallet loading capacity (Dual table) |
Kg |
500 |
600 |
1000 |
1500 |
3000 |
||
Max. dia. of workpiece |
mm |
650 |
700 |
850 |
950 |
1250 |
1900 |
|
Max.height of workpiece |
mm |
640 |
850 |
950 |
1000 |
1300 |
1500 |
|
Number of change pallets |
number |
2 |
2 |
2 |
2 |
|||
Pallet Change time |
second |
12 |
14 |
15 |
15 |
35 |
||
Travel |
X-axis(Column) |
mm |
700 |
800 |
1000 |
1300 |
1700 |
|
Y-axis (Headstock) |
mm |
600 |
700 |
800 |
1000 |
1350 |
||
Z-axis (Worktable) |
mm |
600 |
800 |
800 |
1100 |
1400 |
||
Spindle center to pallet surface |
mm |
50 ~ 650 |
50 ~ 750 |
25 ~ 825 |
50 ~ 1050 |
100 ~ 1450 |
||
Spindle nose to pallet center |
mm |
150 ~ 750 |
150 ~ 950 |
150 ~ 950 |
200 ~ 1300 |
200 ~ 1600 |
||
Spindle |
Spindle taper |
- |
NO 40 (Optional NO 50) |
NO 50 |
NO 50 |
NO 50 |
NO 50 |
|
Spindle rpm |
r/min |
Standard 20 ~ 6000 Optional 20 ~ 8000 |
Standard 20 ~ 6000 Optional 20 ~ 8000 |
Standard 20 ~ 5000 Optional 20 ~ 8000 |
Standard 20 ~ 5000 Optional 20 ~ 8000 |
|||
Speed selection |
- |
Programmable in the full range |
Programmable in the full range |
Programmable in the full range |
Programmable in the full range |
|||
Spindle motor |
Kw |
11/15 |
18.5/22 |
15/18.5 |
18.5/22 |
18.5/22 30/37 |
30/37 |
|
Max. spindle torque |
N.m |
95 |
520 |
118 |
520 |
520 or 1240(add ZF reducer) |
310 or 1240(add ZF reducer) |
|
Tool Magazine |
Tool pockets |
- |
32 (Optional 40,60) |
40 (Optional 60,80,120) |
40 (Optional 60,80,100,120,160) |
40 (Optional 60,80,100,120,160) |
||
Type of tool shank |
- |
ISO40BT50 (Optional ISO50/BT50) |
BT50 (Optional ISO50/SK50) |
BT50 (Optional ISO50/SK50) |
BT50 (Optional ISO50/SK50/JT50) |
BT50 (Optional ISO50/SK50/JT50) |
||
Max. tool diameter |
mm |
75BT50 (Optional 125) 130 (Optional 250) |
125 (With tool at adjacent pocket) 250 (Without tool at adjacent pocket)
|
125 (With tool at adjacent pocket) 250 (Without tool at adjacent pocket) |
120 (With tool at adjacent pocket) 250 (Without tool at adjacent pocket) |
120 (With tool at adjacent pocket) 250 (Without tool at adjacent pocket) |
||
Max. tool length |
mm |
300 |
400 |
400 |
450 |
480 |
600 |
|
Max. individual tool weight |
Kg |
10 (Optional 15) |
20 |
25 |
20 |
25 |
25 |
|
Tool change time (T to T) |
second |
2.5 |
3.5 |
4.5 |
3.5 |
3.5 |
3 |
|
Tool selection |
- |
stochastic,bi-directional |
stochastic,bi-directional |
Fixed tool station |
Fixed tool station |
|||
Driven for controllable axes |
Feedrate |
m/min |
0 ~ 15 |
0 ~ 20 |
0 ~ 15 |
0 ~ 20 |
20 |
0 ~ 20 |
Rapid travel |
m/min |
30 |
45 |
24 |
45 |
40 |
50 |
|
Servo motor |
kw |
3 |
4 |
4 |
6 |
77 |
||
B-axis servo motor |
kw |
1.6 |
3 |
3 |
4 |
4 |
||
Location feedback (X,Y,Z,B axes) |
- |
Encoder(Grating scale) |
Encoder(Grating scale) |
Encoder(Grating scale) |
(X,Y,Z)Liner Grating scale (A,B)Rotary Grating scale |
|||
Min. Increment(X,Y,Z) |
- |
0.001(Optional 0.0001) |
0.001(Optional 0.0001) |
0.001(Optional 0.0001) |
0.001(Optional 0.0001) |
|||
Min.Increment (A,B) |
- |
0.001(Optional 0.0001) |
0.001(Optional 0.0001) |
0.001(Optional 0.0001) |
0.001(Optional 0.0001) |
|||
Machine Accuracy |
Positioning accuracy (X/Y/Z) |
mm |
THM6350 0.008 TH6350 0.015 |
THMA6350 0.008 TH6350 0.015 |
THM6363 0.008 TH6350 0.015 |
THMA6363 0.008 THA6350 0.015 |
THM6380 0.008 TH6380 0.015 |
0.08 (VDI/DGQ 3441) |
Repeatability (X/Y/Z) |
mm |
THM6350 0.005 TH6350 0.008 |
THMA6350 0.004 TH6350 0.008 |
THM6363 0.005 TH6363 0.008 |
THMA6363 0.004 THA6363 0.008 |
THM6380 0.005 TH6380 0.008 |
0.04 (VDI/DGQ 3441) |
|
B-axis indexing |
“ |
THM6350 6 TH6350 8 |
THMA6350 6 TH6350 8 |
THM6363 6 TH6363 8 |
THMA6363 6 THA6363 8 |
THM6380 8 TH6380 10 |
8 (VDI/DGQ 3441) |
|
B-axis indexing repeatability |
“ |
THM6350 3 TH6350 5 |
THMA6350 3 TH6350 4 |
THM6363 3 TH6363 5 |
THMA6363 3 THA6363 4 |
THM6380 5 TH6380 7 |
5 (VDI/DGQ 3441) |
|
Geometric accuracy Standard |
- |
Precision level:JB/T 8772.1-1998 Ordinary level:JB/T 8771.1-1998 |
Precision level:JB/T 8772.1-1998 Ordinary level:JB/T 8771.1-1998 |
Precision level:JB/T 8772.1-1998 Ordinary level:JB/T 8771.1-1998 |
Precision level:JB/T 8772.1-1998 Ordinary level:JB/T 8771.1-1998 |
|||
Installation specification |
Machine net weight |
Ton |
12 |
15 |
15 |
16 |
22 |
30 |
Total power consumption |
KVA |
40 |
60 |
60 |
100 |
120 |
||
Power supply |
- |
360V/50Hz/Tri-phase |
360V/50Hz/Tri-phase |
360V/50Hz/Tri-phase |
360V/50Hz/Tri-phase |
|||
Air supply |
MPa |
0.6 |
0.6 |
0.6 |
0.6 |
|||
Air flow-rate |
L/min |
280 |
280 |
280 |
280 |
|||
Electrical control system |
Control System |
- |
FANUC OIMC (Optional FANUC 18i SIEMES 8400) |
FANUC OIMC (Optional FANUC 18i SIEMES 8400) |
FANUC OIMC (Optional FANUC 18i SIEMES 8400) |
FANUC OIMC (Optional FANUC 18i SIEMES 8400) |
Characteristic
1.Machine structure
High Rigidity, Heavy Duty T-Shape Bed Configuration .
The Column moves in Transverse direction (X-axis)
The Headstock moves in Vertical direction (Y-axis)
The Worktable moves in Longitudinal direction (Z-axis) This structure ensures optimum spindle rigidity and machining linearity.
Meenhanite cast iron machine bed, column and slide design are FEA-refined for optimum rigidity and thermo-symmetry.
Cutting Zone
Easy accessibility and clear visibility.
Machine Layout
The bed and column are rationally ribbed to minimize vibration during cutting. This structure gives additional torsibility and rigidity.
2.Headstock And Spindle
P2H (Accuracy Grade) triple combined front bearings and dual combined back bearings are all lubricated by long effective greasy to minimize heat generation. The spindle is driven by arc timing belt and force cooled by outside loop (Optional center cooling spindle.and/or built-in motor spindle).
Headstock Balance
A hydraulic balancing system is designed for headstock(Yaxis) movement to ensure Y-axis accuracy.
Rigid Tapping
The encoder synchronizes Z-axis movement and spindle rotation. This enable the tapping tool to withdraw from the tapping hole quicker than it enter. Thus saves cycle time
3.Auto Tool Changer (ATC)
Cam type manipulator with single arm and dual claw which provide 25kg tool change capacity. Tool to tool change time 3.5 seconds. No.50 tool shank (BT50, ISO50 and SK50 are standard for selection). Chain drive tool magazine with 40 tools capacity. Optional 60 pockets, 80 pockets, 100 pockets, 120 pockets and 160 pockets magazine.
4.Rotary Worktable (B-Axis)
High precision roller bearing assembly for rotary axes supporting. HEIDENHAIN incremental angle encoder for full-closed-loop detecting which ensure B-axis indexing accuracy.
Tiltable A Axis
Specially designed tiltable compound worktables ( φ 500,φ630,φ800, φ 1000, φ1100) to meet customer’s various requirement. Swing angle ranging from 0° to 90°.
5.Linear Axes
The linear guide ways are all pre-tightened to zero clearance and full bearing capability on all directions. This bring 40m/min. rapid feedrate, accurate positioning and creeping free low speed movement on Z-axis at heavy cutting load. Each linear rolling guide way are individually lubricated and all surface are precisely scraped to improve fitting accuracy.
6.Coupling
The servomotors are coupled directly to ball screw with steel coupling to eliminate ball screw deflection even at heavy load. This greatly improves the positioning accuracy and working accuracy.
7.Pallet Clamping System
4 taper pins with hydraulic locking are designed for pallet positioning. This structures ensures high positioning accuracy and large locking force.
8.Cooling, Chip Removing And Machine Enclosure
Twin screw chip conveyer is designed for the machine. Slant guide way cover to lead the chip to the chip tank. All those construction make chip conveying more convenient.
Chip Conveyer
Full closed machine cover features clean and bright outlook. Unique protection door make the operation more easy and human friendly. (Various types chip conveyers may be adopted for different versions of machines.)
Guideway Covers
Telescope steel cover for X, Y and Z- guideways which helps to improve the rapid feed-rate and make the machine better protected and more bright in outlook.
Machine configuration |
|
Main machine |
Standard |
Full closed machine cover |
Standard |
Work lamp |
Standard |
Tri-color Iamp |
Standard |
Chip remover |
Standard |
Tool cooling system |
Standard |
Self-diagnosable system |
Standard |
ATC cover |
Standard |
Pallet positioning hole blowing device |
Standard |
Spindle hole blowing device |
Standard |
Manual pulse generator |
Standard |
Self power brake system |
Standard |
Manual tool change device (tool magazine) |
Standard |
Manual tool change device (spindle) |
Standard |
Tool kit |
Standard |
Automatic Lubrication system |
Standard |
Square block |
Standard |
Cylindrical contour block |
Standard |
Pallet cleaning device |
Standard |
Chain-type chip remover and carrier |
Standard |
Coolant degreasing device |
Standard |
Squirt gun |
Optional |
Manual blowing gun |
Optional |
Tool probe |
Optional |
Workpiece probe |
Optional |
Rota window |
Optional |
Product detail pictures:
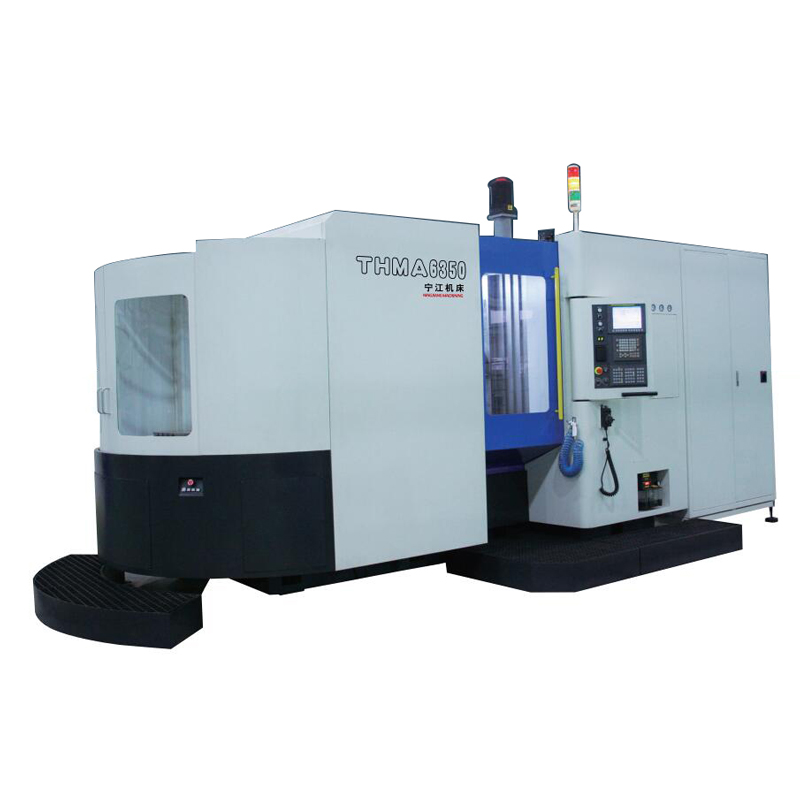

Related Product Guide:
All we do is usually connected with our tenet " Consumer initial, Rely on 1st, devoting around the food stuff packaging and environmental safety for YUNNAN CNC Lathe – NINGJIANG High Performance Horizontal Machining Center TH(M)6350 TH(M)A6350 TH(M)6363 TH(M)A6363 THM6380 THM631000 – Maiouke , The product will supply to all over the world, such as: Czech republic, Brazil, Singapore, We have the best products and professional sales and technical team.With the development of our company, we are able to provide customers best products, good technical support, perfect after-sales service.

Customer service staff and sales man are very patience and they all good at English, product's arrival is also very timely, a good supplier.
